—— Production process ——
XyloSuisse is one of the leaders in the sphere of particle boards and laminated particle boards production in Russian woodworking market.
Features of particle board:
Particle board is made of such wood material as undersized tree, slash wood, wastes of wood processing, etc., such board has been widely applied for furniture, construction, packaging, inner fixture of vehicle and ship, etc.
Particle board is made from small-diameter wood, branches, wood residues and non-wood agricultural residues running through Chip preparation, drying, spreading and hot press sections:
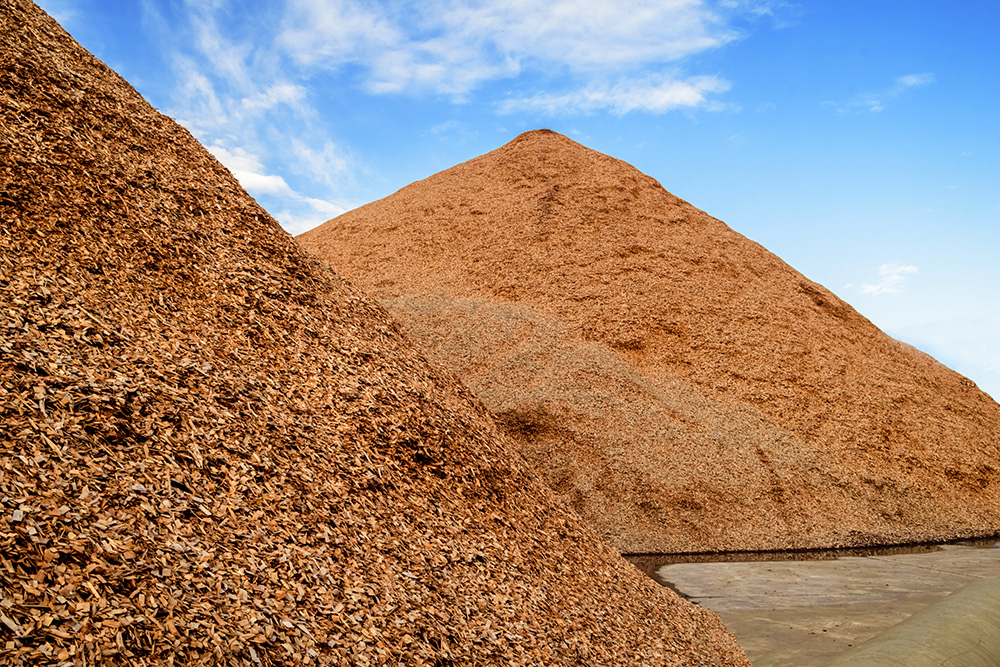
The 1st phase – PREPARATION OF RAW MATERIAL
A particle board is a composite sheet material made by means of compaction of wood particles with non-mineral urea formaldehyde resin in a hot press.
We produce particle boards using high-quality raw materials from local forests and neighboring saw mill plants. Wood raw materials are crashed into wood chips with the help of chipper machine. After processing in special rotary machines wood chips become flakes of necessary size as prescribed by the regulations of technological process. The milled raw flakes are stored in hoppers supplied there by pneumatic and mechanical conveyor.
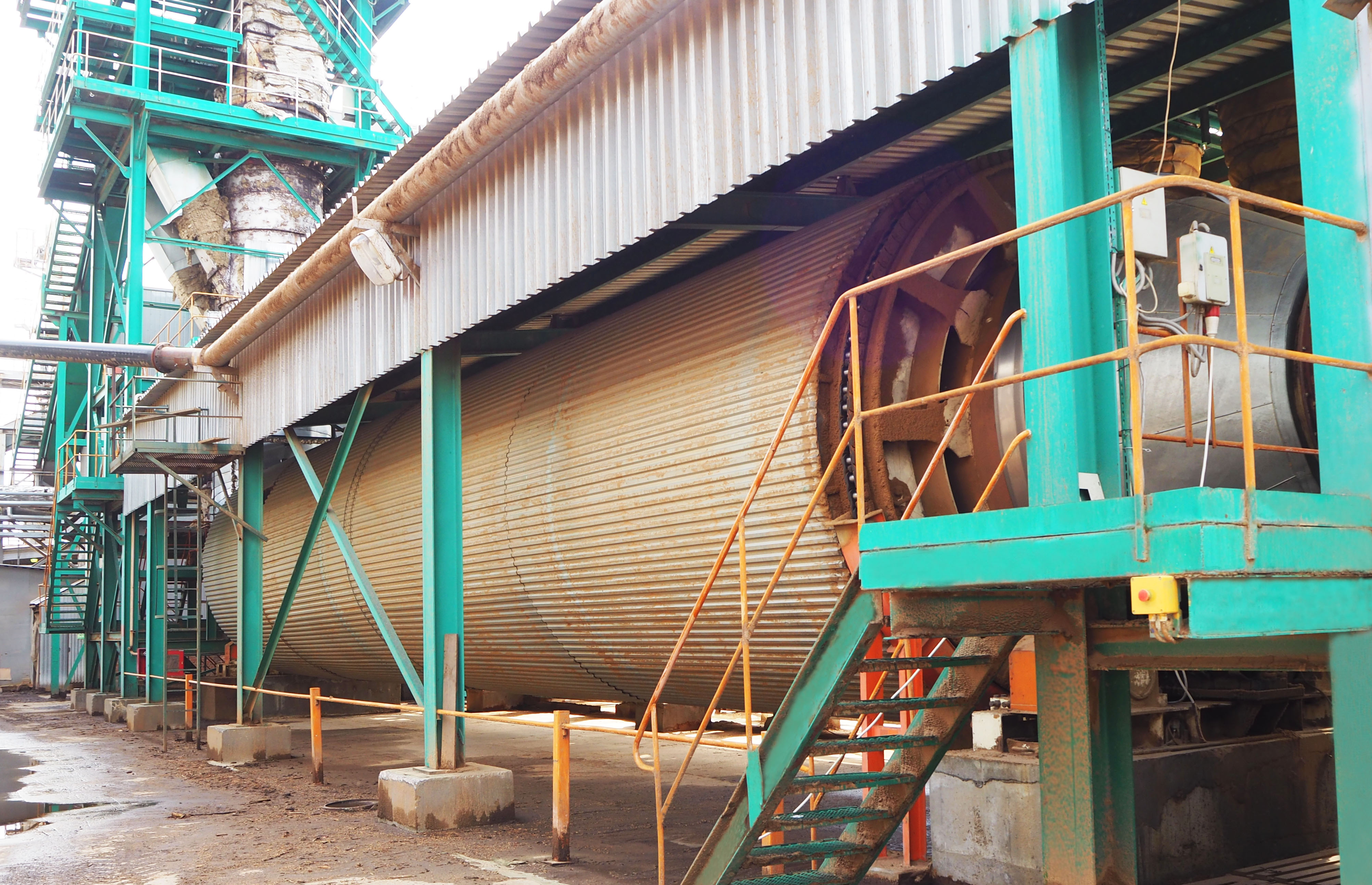
The 2nd phase – DRYING OF RAW MATERIAL
From the hopper raw flakes are fed to the dryer. In the PB production process we use a drum-type dryer.
The flakes are dried up to 2-4 % of moisture level.The drying process goes on by using hot air with the temperature of 600-700 °C in the drum inlet.Then the dried material goes to the next production stage.
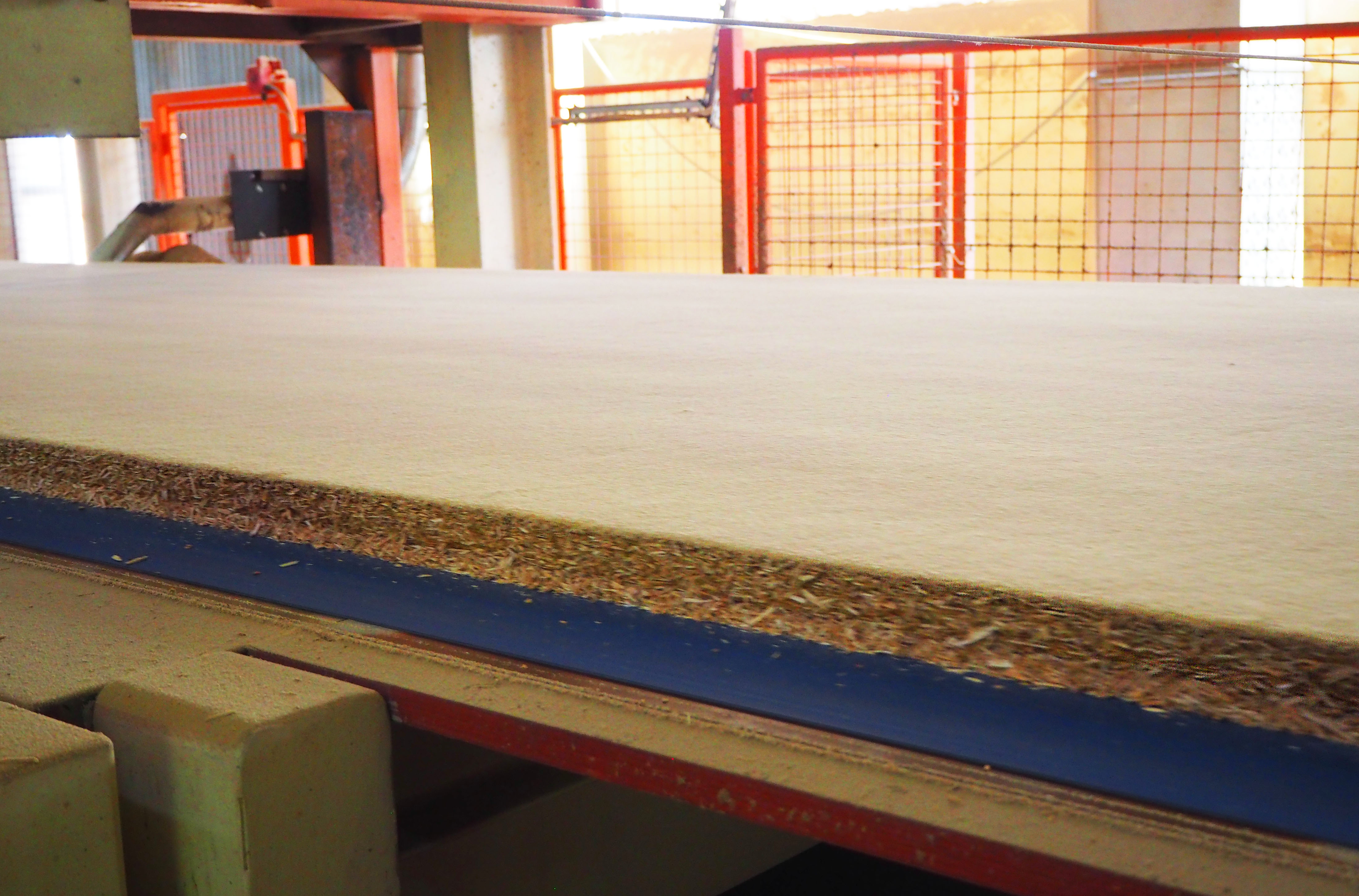
The 3d phase – MAT FORMATION
At this stage the flakes are screened in order to remove all the contaminated particles (stones, sand, metal and non-metal additives) and separated into two different fractions: fines (surface layer) and coarse fraction (core layer). Each fraction is transported to and stored in its individual dry hopper.
Flakes from these hoppers go to the blender that is a special machine to mix flakes and resins accurately.
This stage is very important because the final mechanical property of the board depends mostly on it.
In order to constantly control the correct ratio between wood flakes and resins all the processed materials are monitored by scales and a special computerized system for controlling the quantity of used glue.
The resined flakes of two different sizes then are fed to forming machine that separates the material in order to prepare a mat – fine material goes to the top and bottom layers and the coarse fraction goes to the core layer.
After formation the mat goes into cold pre-press to be prepared for the next stage.
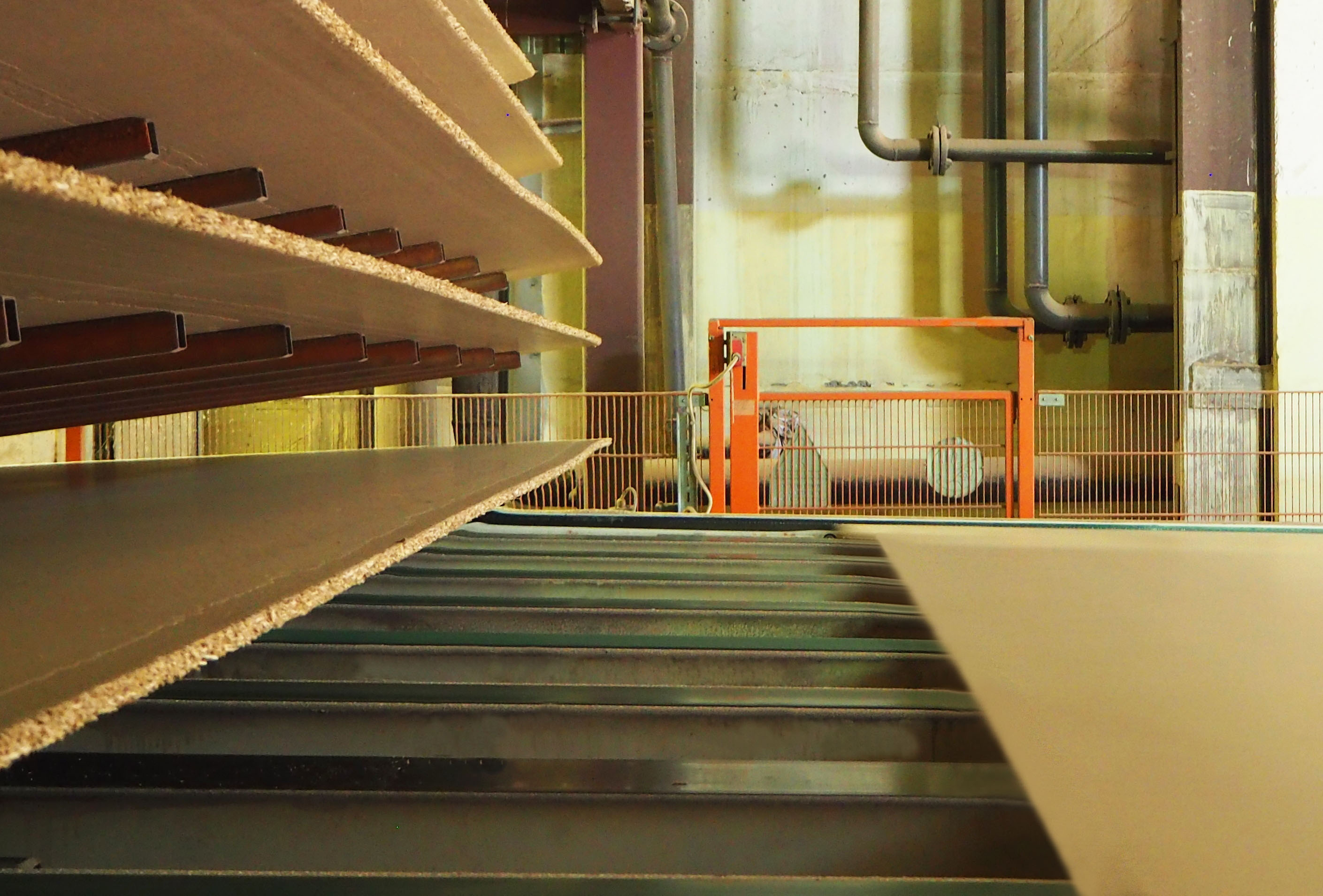
The 4th phase – HOT PRESSING
The pre-pressed flake mat is cut to the definite sizes before going to the hot press and so we receive the so-called master boards of the press plate size.
This is a multi-opening press heated till 180 – 190 °C.
The mat is fed to the press and heated there under a pressure of 35 kg/cm2 until they rich the final thickness and complete technological cycle.
Final thickness of the produced board is controlled by a special computer system.
At the end of technological cycle the board is transferred to the cooling system.
Cooling time depends on the board thickness

The 5th phase – CUTTING AND SANDING
After cooling process the master boars are cut by the automatic trimming machine to achieve the final disposal size.
The fabricated particle boards shall stay in the store for minimum one day in order to be well cooled inside and hardened on the surface.
Further the boards are transferred to the sanding machine. This machine is supposed to sand the surfaces of boards in order to have an accurate thickness and a very clean and smooth surface necessary for the process of lamination.
Melamine faced chipboards are produced using modern European equipment with automated quality control systems for each technological stage.
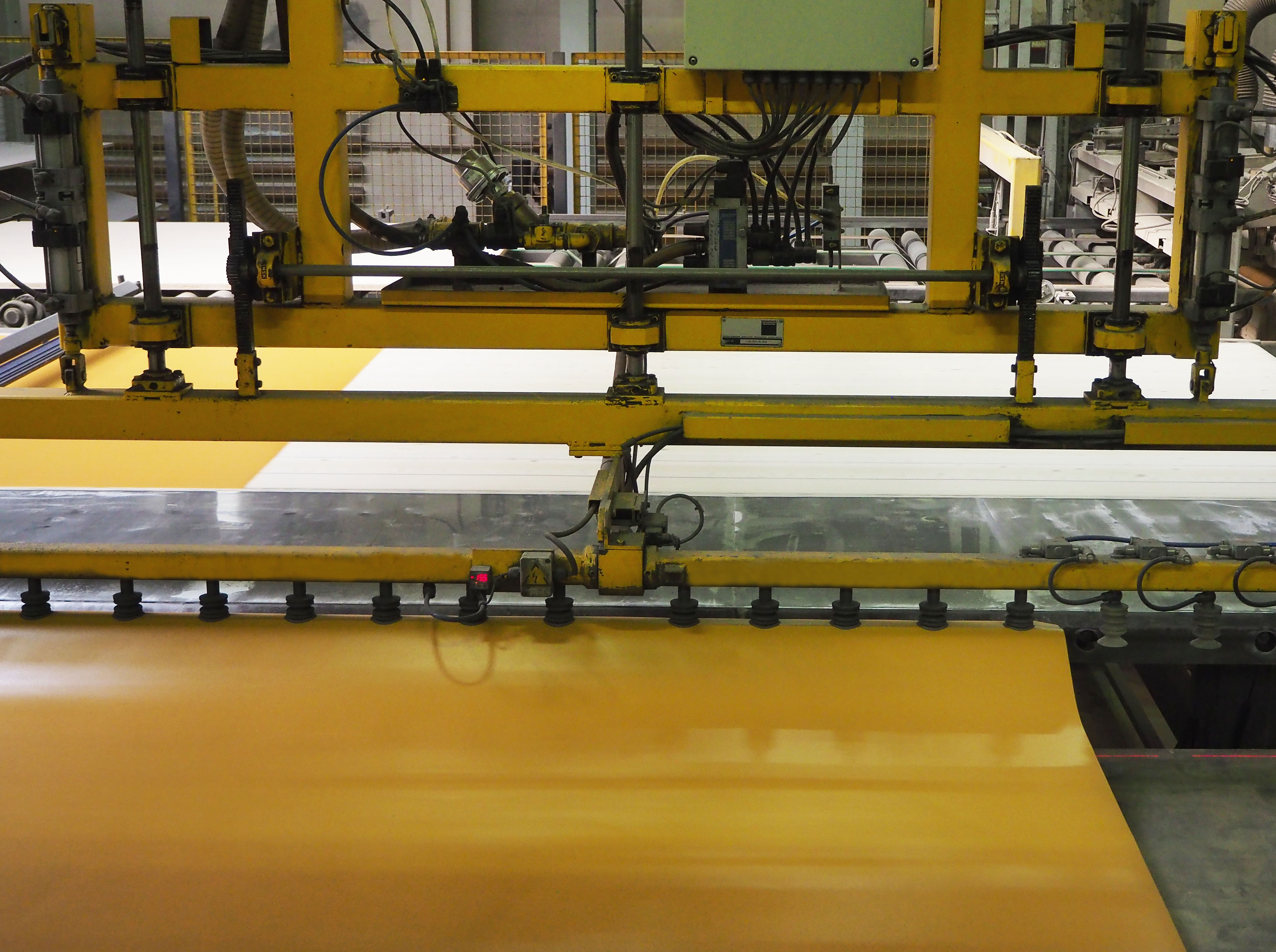
The 1st phase – COATING
For production of laminated boards we use only high-quality sanded boards produced by our plant.
With the help of automatic line the impregnated decorative paper is fixed on the top and bottom surface of the board.
Our company uses decorative impregnated paper treated with melamine resins produced by the world leaders in this field.
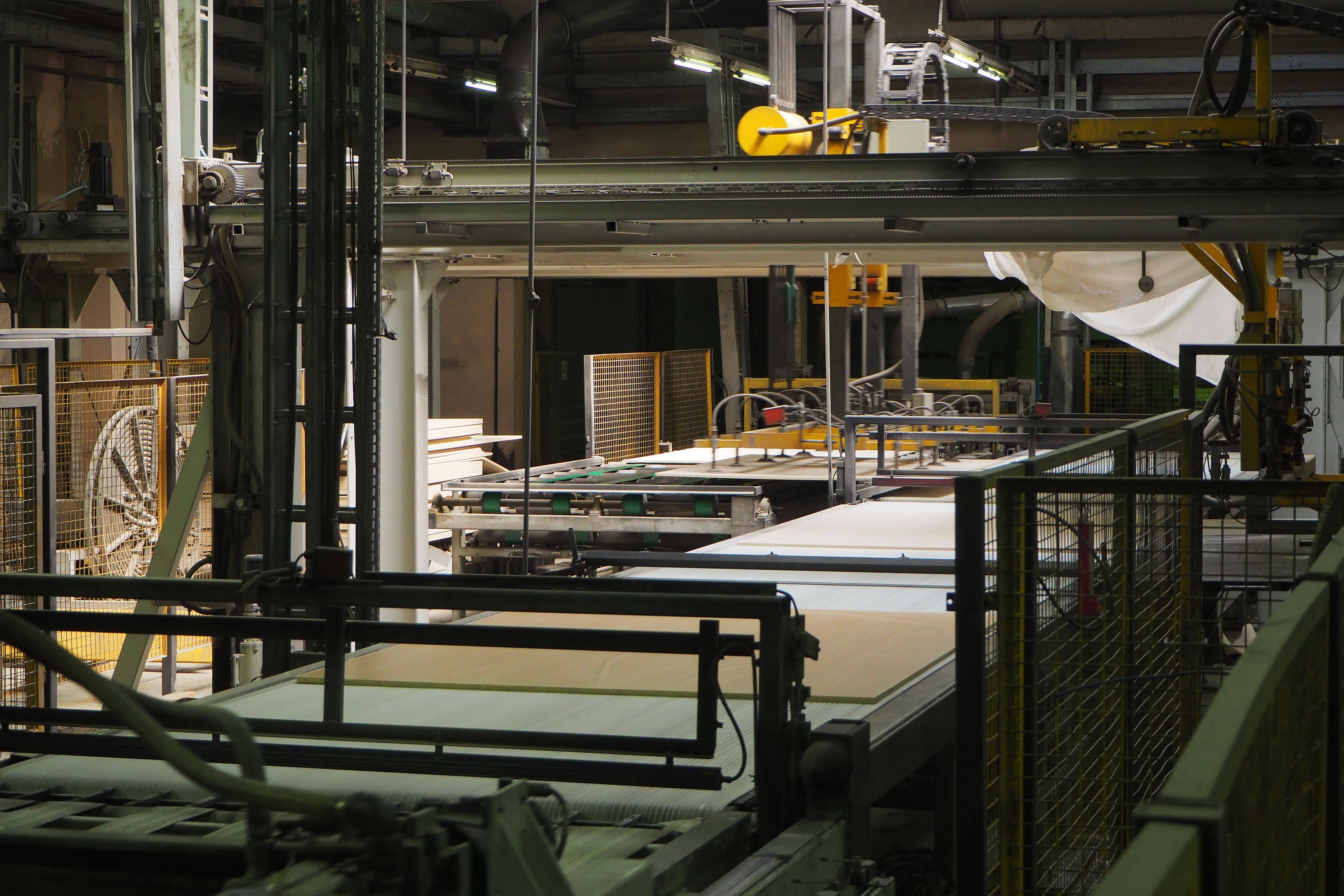
The 2nd phase – PRESSING
During coating the boards are transferred to the short cycle press.
The working pressure of the press is about 20-25 kg/cm2 and the temperature of the heated plates reaches 180 – 200 °C.
Between the hot plates and paper layers there are two chromed grids in order to create the texture of the board surface.
Processed by pressure and temperature the resin inside the impregnated paper melts and acquires the properties of plastic becoming scratch resistant.
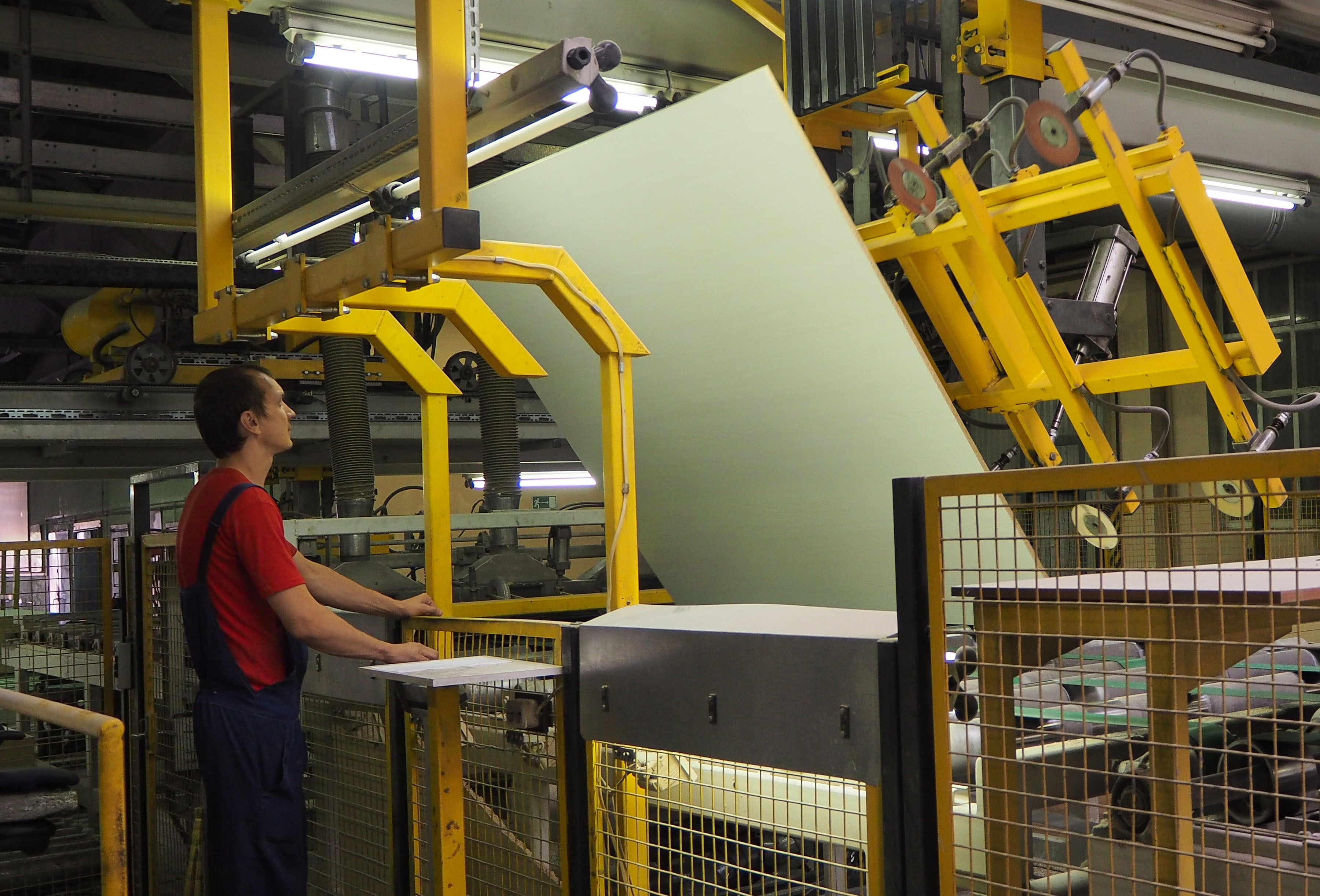
The 3rd phase – QUALITY CONTROL AND STACKING
After pressing the boards are transferred to the control station where visual control is executed by the operator who shall grade the boards by their quality. The perfect boards only shall be stacked to dispatch.
The boards correctly stacked and packed are ready to be sent to the finished-products storage area for further shipping to the client.